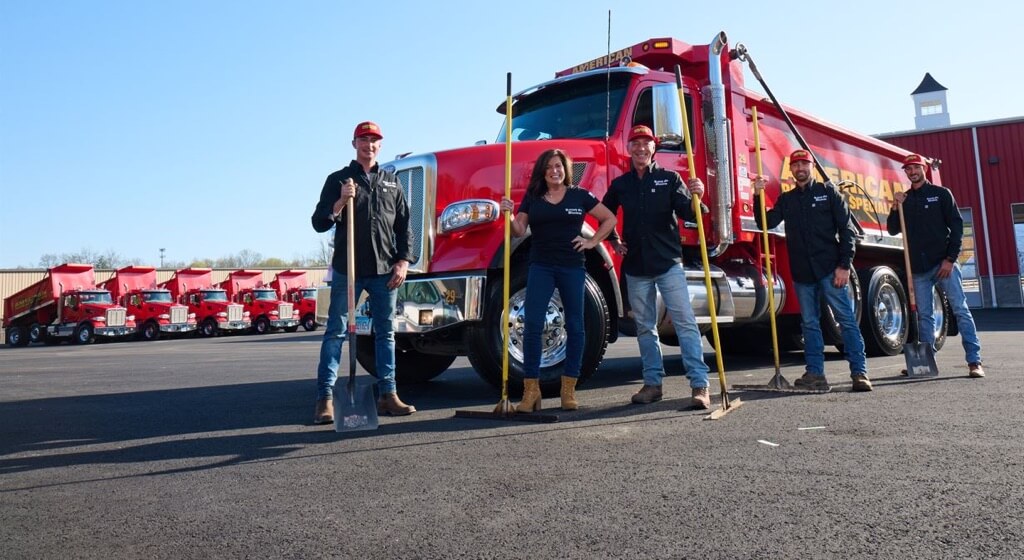
29 Feb APS Makes Winter Work Work
It was more than a decade ago when Bill Stanley, owner/operator of American Pavement Specialists (APS), Danbury, Connecticut, walked into Edward Erhbar Equipment looking to buy two Bagela BA10000 asphalt recyclers.
The event stood out to Greg Harla, partner at Bagela USA/Pavement Recyclers, for two reasons. The first was because this sale would make APS one of the first companies in the United States to own and operate two BA1000s. The second was because of the four young men Bill brought in tow: his sons, Bill Stanley III, 39, Jack Stanley, 37, Josh Stanley, 33, and Matt Stanley, 31.
Harla had been a yellow page ad rep in the early ’90s and called on a very young APS to advertise. Bill’s wife, Colleen, was his main point of contact. “Every time I called on her, it seemed there was one more little one playing with toys on the floor,” he said. “Fast forward to 2010 and Bill walks in with those four little guys—only they weren’t so little anymore.” All four were grown and all four had joined the family business. “[Bill] said, ‘Greg, all I want to do is keep my boys busy in the winter.’”
One catalyst for investing in an asphalt recycler from Bagela was to keep the APS crews busy year round. The inability to keep every member of the crew employed year-round meant more employee turnover for the company. “Across America, the fact most paving companies have to lay off employees in the winter directly affects the quality of laborers and operators we as an industry attract,” Matt said.
According to Bill, there were several reasons behind his decision to expand into asphalt recycling—among them, a way to make use of the company’s millings after it purchased its first milling machine in 2010. However, he added, “The first and most important was year-round work.”
Historically, APS’s region of the northeast experiences up to 16 weeks of winter shutdown. “The industry’s shutdown is definitely the most difficult part of being a paving contractor,” Bill said, adding that to make ends meet paving contractors often must do A.F.B. work (Anything For a Buck). “For APS, nothing was ever enough to make a real profit and hold onto our crews all year round, which has always been our goal.”
Additionally, the inability to keep every member of the crew employed year-round meant more employee turnover. “Every spring feels like we are re-hiring, retraining, re-building, re-starting with a lot of hoping and praying that we can make a solid go of the season,” Bill said. “Fall quickly approaches and you literally have to make everything happen, from making a profit for the season to completing every project to keep your customers happy. Then all in one fell swoop, December rolls around and it’s over.”
Although APS wasn’t in a position to change the way the Connecticut asphalt industry operates in 2011, the company was in a position to change the way it operated by turning asphalt recycling into one of the company’s winter services—and a successful one at that.
Today, not only does APS sell hot patch throughout the winter, but it sold hot patch nearly every day of 2024 at press time. And, the company just produced mix for and placed a 250-ton hot patch for the city of Danbury in the middle of January.
Quality In, Quality Out
In January the city of Danbury had a water main break on Mountain Road, which had just been paved the previous year. The city, APS’s hometown and longtime customer, contacted the company to purchase roughly 250 tons of asphalt to place a temporary patch along a 2,000-foot-long, 4-foot-wide trench.
Matt Stanley is the founder of the Raised on Blacktop brand. He says a core component of the brand is inspiring the new and next generations of asphalt professionals. “Having a brand that represents the common contractor can not only draw the next generation into the industry but also provides our industry with better representation throughout the construction industry as a whole,” Matt said.
“A temporary patch would mean having to pay a contractor to rip it all out and repave it in the spring/summer,” Bill said. “We felt this was a large purchase to call temporary, so we sold them a permanent patch using 100% recycled asphalt, delivered with our auger truck and professionally installed as if it were July and not January.” (For more information about the sustainability of the project and process, check out the sidebar “Green, Lean Recycling Machine”).
Such a robust claim relies on the expertise and equipment to back it up. This begins with replacing the two older Bagelas with a new machine in 2024.
As with any asphalt, the quality of the hot patch APS produced for the project depends heavily on the quality of the material with which it is produced. APS opts to make its hot patch from virgin material left over from the paving jobs it performs in the warmer months.
“As the guy on the paver, sometimes you order that last load and you end up having a couple tons left over,” said Matt Stanley, Bill’s son and the founder of the Raised on Blacktop brand. “It isn’t ideal to have mix left over, but when it happens, we can recycle it come winter.”
APS dumps the leftover mix into a series of 2-ton piles, breaks it up once the material hardens, tarping it when necessary to minimize moisture. “[The Bagela] can produce 8 tons an hour in winter, 10 to 12 in summer,” Matt said, adding that it’s important the material is dry. “If that material is wet, it cuts our numbers in half.”
Matt said elevating the recycler off the ground and its location partially enclosed in APS’s old shed also improves the quality of the mix by retaining more heat. APS loads the machine with its John Deere 310 SL and John Deere 333G track loader, checking the temperature regularly with a temperature gauge. “I want around 300 to 350 degrees Fahrenheit,” Matt said. “Once I get below 300, I stop adding material because I want to let that material inside heat up.”
As material is produced, it is weighed with a scale and bucket and loaded into APS’s custom Trout River auger trucks. (Read more about these trucks in the sidebar, “Partnering on the ‘Perfect Truck’”). “If we load out around 300 to 350 degrees, we figure it’ll be around 275 coming out of the truck [at the job site].”
The new 10-ton trucks played a key role in the success of the Mountain Road trench and other cold-weather repairs. “The tarp system on these trucks is superior to any tarp system I’ve seen on the market,” Matt said. During the 2023 paving season, APS consistently saw mix from the Trout River trucks arrive at the job site a full 10 to 15 degrees warmer than its other trucks.
But, retaining heat when patching in winter means more than tying down the tarp. The live bottom trucks are equipped with augers and a conveyor at the back to directly deliver mix to the patch. “We aren’t dumping it on the ground, we aren’t handling it too much; the mix goes right from truck to patch,” Matt said.
In 2024, APS replaced its two older Bagelas with a new machine. The company sold
hot patch all winter long, including using 250 tons of the mix for its trench project
in Danbury, Connecticut, in January 2024.
The efficiency of this process also makes it less labor-intensive, he added. “When we deliver [hot patch] for our customers with these trucks, they might have six or seven laborers waiting to rake the asphalt,” Matt said. With the auger truck, jobs often require only one person raking.
Bill said the auger trucks were a perfect fit for the company’s trench job on Mountain Road. “The delivery is so quick, we got the job done in just two and a half days,” he said. “This is the 21st Century way to put asphalt into a trench.”
Cold-Weather Quality
Although the Trout River trucks were critical to the success of the project, APS had to prioritize quality every step of the way. The city repaired the trench and placed gravel one week before APS came out to pave, but did final preparations immediately ahead of the crew. “They took off the mud and frost, not exposing the gravel we were paving on until that morning,” Bill said.
The crew placed between 3 and 4 inches of asphalt into the trench. Normally, they’d put that down in two courses, but decided one course would help retain heat and therefore improve compaction given the 45-degree temperature on the days of paving.
It was also important to keep moving. “With winter paving, you have to pave fast and roll it immediately,” Bill said. The haul truck driver managed a consistent speed, closely watching the crew placing the asphalt in the rearview mirror. On the ground behind the truck, Bill controlled the conveyor speed to ensure material flow. “Since this trench is the same width and thickness, we barely had to do anything,” he added.
During the 2023 paving season, APS consistently
saw mix from the Trout River trucks arrive at
the job site a full 10 to 15 degrees warmer than
what was delivered in its other trucks.
Immediately behind the truck came APS’s Hamm HD12 roller. “It’s not easy to pave in winter,” Bill said, “but we took our time, brought in our two Trout River trucks, extra laborers and a 3-ton roller (not just a plate compactor).”
Also ahead of paving, APS sprayed hot tack on the sides and bottom of the trench. “Our biggest concern on this job was raveling, so we did everything we could to help prevent that,” Bill said. “This job shouldn’t have any structural problems, so as long as it doesn’t ravel, our guys won’t have to do this all over again come spring.”
So far, the trench is holding up well—and that’s saying something. “We had a hell of a test on this project,” Bill said. “We finished the project on a Friday. On Saturday we had a Nor’easter with 4 inches of wet, heavy snow. The road was plowed and sanded. Then, Sunday it warmed up to 50 degrees, the snow melted, the ground was saturated and we got another 4 inches of rain. That’s bad for any pavement, but especially fresh pavement.”
However, when Bill rode the project a few weeks after paving, there were no defects. “With how it held up, you would never guess this was paved in January with recycled asphalt,” he said. “We’ll revisit it in the spring and take care of any defects, but we hope that if it’s good after what it’s already been through that it’ll still be good come spring.”
On the Mountain Road project in January 2024, APS
used its custom Trout River auger trucks. Although APS
uses the trucks on projects throughout the paving season
(as seen here), the new 10-ton trucks played a key role
in the success of the Mountain Road trench and other
cold-weather repairs.
Room to Improve
Despite the success of the project, Bill identified one way it could have gone better: “If we had hot mix asphalt.”
“If this same repair happened a few years ago, it would definitely have stayed gravel all winter or maybe they’d put in cold patch,” Bill said. “Hot patch gives us an alternative to those methods, but I think it would have gone even better with HMA.”
Back when APS purchased its first two Bagelas in 2010, the company wasn’t in a position to change the industry. Now, it’s one of the most popular social media influencers in the asphalt industry, with nearly 300,000 followers across all platforms for APS and Raised on Blacktop, and Bill wants to use that position to effect change.
“Contractors like us have to have access to quality hot mix asphalt year-round,” he said. “The fact that we’re making and selling hot patch all winter long, that we’re laying quality 250-ton projects in January, that New York City one hour away from us has HMA plants running year-round illustrates that there’s plenty of need.”
“Completely shutting down all winter is 20th Century thinking,” Bill said, adding that excavators, frost blankets, improved heating elements and other innovations have made quality more achievable for winter work.
Of course, he acknowledges that winter work will be more costly, slower, and with less margin for error. “There are a thousand reasons why people say you can’t pave in cold weather—and they’re all to some extent true,” Bill said, adding that there are many projects he’d never consider paving in winter. “However, there are circumstances where people need asphalt in winter and there are days in winter where we can and should be working. This [Mountain Road] project is living proof.”
Whether or not the industry answers Bill’s call, APS will continue to produce hot patch year-round. “We’re not getting rich off this; to me, it’s about answering the call from our customers,” Bill said. “When they ask if we can make blacktop in winter, our answer is going to be ‘Hell yeah’.”
Over time, Bill anticipates the shutdown season in colder climates will get shorter and shorter as technology continues to improve. “I truly believe it won’t be long before winter will merely be a ‘slow season’ and there will be more opportunity for asphalt to become a four-season business.”
Bill Stanley, right, hopes the success of American Pavement Specialists’ recent winter
trench project in Danbury, Connecticut, will encourage the industry to change
with the times and provide access to hot mix asphalt year round.
Making a Movement
It’s a sentiment shared by his son Matt, who in addition to working at APS founded the brand Raised on Blacktop. “By sticking our necks out to experiment with new practices, we’ve shown our customers and municipalities that paving in the off-season is possible,” Matt said.
APS has long been an industry trailblazer on social media, starting its account when the demand for asphalt-related influencers had yet to be proven. They see trailblazing on this effort as no different.
“We’ve really leaned into our role [as trailblazers] over the past 10 years we’ve been on social media,” Matt said. He hopes the success of APS’s hot patch operation in general and the Mountain Road project in particular will improve stability in the asphalt industry, “especially for young business owners, where long off-seasons could kill a company,” he said. “But even more so, [I hope it stabilizes] the labor force.”
“Across America, the fact most paving companies have to lay off employees in the winter directly affects the quality of laborers and operators we as an industry attract,” Matt said. Inspiring the next generation of asphalt professionals is a core component of the Raised on Blacktop brand.
“Seeing the look on a kid’s face when they’re wearing a brand that represents them or what their parents do for a living is what fuels me,” Matt said. “Having a brand that represents the common contractor can not only draw the next generation into the industry but also just provide our industry with better representation throughout the construction industry as a whole.”
Harla with Pavement Recyclers has seen the evolution of Raised on Blacktop, from watching little boys playing with toy trucks to witnessing grown men helping design better haul trucks. “They’re bringing efficiencies and profitability and new ideas to the next generation. …They’re bringing solutions to our industry,” he said. “Raised on blacktop is a movement.”
Sorry, the comment form is closed at this time.